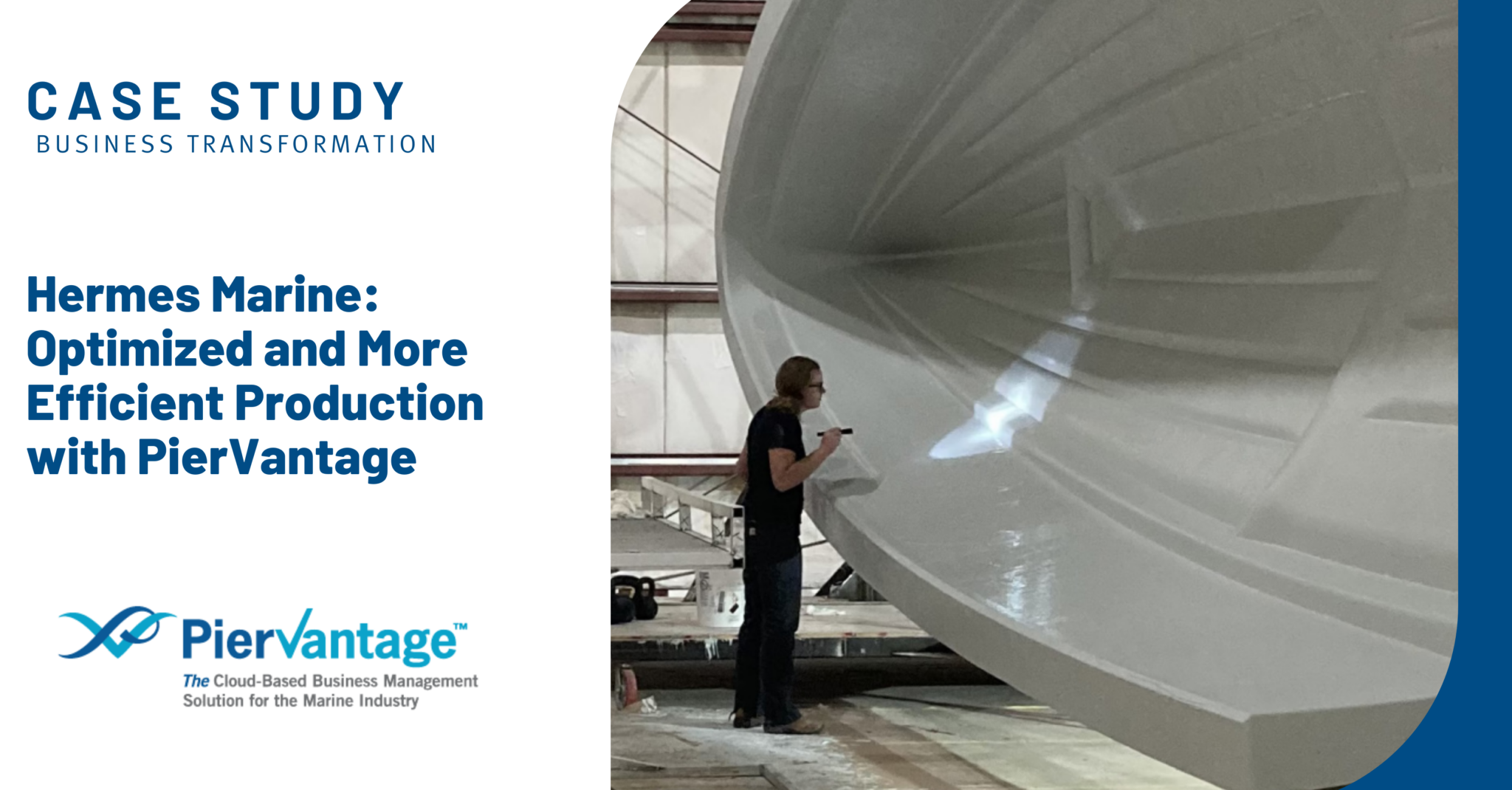
While start-up Hermes Marine LLC is new to the boat building market, the team behind the scenes is highly experienced and all-too-familiar with potential waves that could deter production success.
The Edenton, North Carolina-based company is focused on building the Saxdor 320 GTO fiberglass yacht designed by Saxdor in Helsinki, Finland. Hermes Marine will offer three different configuration fiberglass boats from scratch using Saxdor boat molds. The boats will be sold through dealerships, which have Saxdor 320 GTOs on order in the first quarter 2022. The first boat is on track to be completed in early summer and production will quickly find a steady rhythm to meet increasing demand. But it’s not the ability to build quality boats that concerned the executive leadership of this firm; it was managing production with efficiency.
Challenge: Reliance on Disconnected Data
In the company’s earliest days, leadership looked to Frank Edwards, an industry veteran production engineer and manager. With over three decades of experience at companies that include Hatteras Yachts, Gunboat, Bertram Yachts and MJM Yachts, he has seen just about every snag that can derail smooth boat building operations.
Early in his time with Hermes, he noted that the team was already becoming reliant on spreadsheets—a common, though cumbersome approach to production activities. Edwards said, “To meet the production goals that leadership has in mind, we needed a solution that could
track financials, materials, stock, everything that goes into building boats.”
However, he also recognized that the challenge with today’s platforms is that they are often high dollar, complex investments that require extensive customization and are not easy to use.
“I’ve been through this before,” he said. “Companies spend hundreds of thousands of dollars on a solution that doesn’t get used, largely because it’s not intuitive so people don’t use it.”
Solution: Intuitive and Technically Advanced
Edwards recommended PierVantage, a cloud-based marine management solution designed to simplify jobestimation, work management and invoicing, reduce inventory carrying costs and increase the efficiency and profitability of operations. Purpose-built for the boat builders and commercial marine operations, PierVantage includes features and functionality that ranges from work management, workforce scheduling and project templates to purchase order and inventory control modules as well as accounting and reporting capabilities.
Edwards said, “Besides the all-important operational and financial management modules, I like the platform because I knew everyone in the company, even those new to engineering and production process, would see positive value from the system with just a little training.”
By March 2022, PierVantage had been implemented as a core component of the company’s rapidly growing operations.
Benefits: Production Proficiency and Seamless Workflows
Today, PierVantage is starting to be used by a number of key people in the Hermes boat production process. With regard to PierVantage, the team currently relies largely on the Purchase Order Entry, Inventory Control, Work Order Tracking, and Reporting modules.
Edwards explained, “Inventory management is big because we’re using part numbers from our partners, who happen to be European. We were working off of paper purchase orders in the early days, which would become an obstacle once production ramped up. With PierVantage, we can track vendors, stock, purchase orders, labor costs and so much more—and it’s all visible as a report or on the dashboard.”
He noted that the Hermes warehouse manager inputs all parts in the system as those products arrive, and with the technology, she’s able to issue and track all materials as they move from the warehouse to the production line with ease and accuracy.
When asked about company-wide uses, Edwards is quick to say that it is coming. “Like any start-up, time demands on everyone is high. However, this is a tool that can make every job, not just material tracking, easier. For me, the automated reporting is especially great. One of the executive teams has a question about inventory, I click a couple buttons and it’s
there,” he added.
Hermes recently promoted a full-time head of production and she’s beginning to learn the system as well. Edwards concluded, “There’s so much functionality in this platform to help us streamline our operations. I see us taking advantage of labor tracking, scheduling and project management in the near future. It’s exciting to see our capabilities come together to bring our brand to market, as well as realizing the technology’s ability to streamline our workflows with such ease. I personally would never go back to conventional, paper-based methods.”